Reduzierung des Ausmaßes und der Häufigkeit von Anlagenstillständen und Verringerung der Risiken für ungeplante Stillstände und Unfälle
Eine kontinuierliche, fortlaufende Produktion kann durch den Einsatz spezieller nicht-invasiver Inspektionen (NII) im laufenden Betrieb erreicht werden. Dies bedeutet, dass Betreiber ihre Anlagen nicht abschalten müssen, um den Zustand kritischer Anlagen zu überprüfen.
Vor allem in der petrochemischen Industrie sowie in der Prozessindustrie, Öl- & Gasindustrie und der konventionellen Energiewirtschaft ist die regelmäßige Überprüfung von Industrieanlagen erforderlich. Kritische Anlagen (wie z. B. Transportpipelines und Druckgeräte) können aufgrund von Brand- und Explosionsgefahr und der damit verbundenen Risiken eine Gefahr für Mensch und Umwelt darstellen. Mit zunehmendem Alter können Industrieanlagen und Drucksysteme aufgrund von Korrosion und verfahrensbedingten Reaktionen schneller verschleißen. Es können schwerwiegende Defekte auftreten, die ungeplante Abschaltungen mit langen Stillstandszeiten zur Folge haben und zu ernsthaften Risiken für Sicherheit, Gesundheit und Umwelt führen können. Um diese Risiken zu vermeiden, wird eine regelmäßige Inspektion kritischer Anlagen empfohlen.
Herausforderung: Erkennung und Bewertung von Defekten bei laufendem Betrieb
Die Bewertung von Betriebsschäden ist in den ZfP-Richtlinien und -Standards nicht geregelt. Unsere erfahrenen ZfP-Expertinnen und Experten können jedoch die richtigen Prüfmethoden basierend auf Ihrem speziellen Einsatzfall anwenden, so dass Unregelmäßigkeiten und Betriebsdefekte in Bauteilen frühzeitig und ohne unnötige Unterbrechung Ihrer Produktionsabläufe erkannt werden können. Dank der präzisen Fehlererkennung können defekte Materialien repariert oder ersetzt werden, bevor größere Schäden auftreten.
Bewältigung spezifischer Herausforderungen bei kontinuierlichem Anlagenbetrieb
Als Anlagenbesitzer oder -betreiber stehen Sie vor besonderen Herausforderungen, wenn Sie Unterbrechungen und Stillstände in Ihrer Produktion minimieren wollen:
- Unkontrollierte Risiken: Außerplanmäßige Abschaltungen können die Folge unkontrollierter oder schlecht gemanagter Risiken sein (z. B. Havarien wie Ölaustritt, Explosionsgefahr).
- Sicherheitsrisiken beim Arbeiten an laufenden Anlagen: Bei der Inspektion von Anlagen, die in Betrieb sind, sind einige Risiken zu beachten. Inspektorinnen und Inspektoren und andere Verantwortliche sind bei der Arbeit an laufenden Anlagen Sicherheitsrisiken ausgesetzt.
- Umweltverschmutzung und Nachhaltigkeit: Zusätzlich zu den damit verbundenen Sicherheitsrisiken ist die Entfernung von Produktrückständen und die Reinigung der Anlagen zeitaufwändig und kann zu einer hohen Umweltbelastung z. B. zu Ölverschmutzung und chemischen Abfällen führen.
- Außerplanmäßige Abschaltungen mit langen Stillstandszeiten: Durch unentdeckte Defekte verursachte, ungeplante Stillstände sind aufgrund von Produktionsausfällen und Notreparaturen mit hohen Kosten verbunden. Bei einer außerplanmäßigen Abschaltung muss der Anlagenbetreiber zunächst die Ursache des Defekts ermitteln, um ihn zu beheben. Dies kann ein langwieriger Prozess sein. Der Ausfall kritischer Komponenten mit langen Lieferzeiten kann dazu führen, dass eine Anlage über einen längeren Zeitraum außer Betrieb ist.
- Vorbereitung auf geplante Abschaltungen und Reparaturen: Im Gegensatz zu ungeplanten Stillständen können Anlagenbetreiber die Produktion auch gezielt anhalten, um wiederkehrende Inspektionen durchzuführen. Das Management von Maßnahmen während des Turnarounds ist wesentlich schwieriger, wenn es keine detaillierte Planung gibt, die auf genauen Vor-Informationen basiert. Ohne aktuelle Inspektionsdaten ist es schwierig, den Inspektions- und Wartungsumfang genau zu beurteilen. Daher können sich geplante Abschaltungen wesentlich länger hinziehen. Bei Anlagen, bei denen Reparaturen zu erwarten sind, ermöglichen nicht-invasive Inspektionen (NII) die Durchführung von Inspektionen vor der Abschaltung der Anlage. Dadurch kann das Ausmaß der erforderlichen Reparaturen und Wartungsarbeiten vorab bestätigt werden.
- Alternde und stark beanspruchte Anlagen sind anfälliger für Mängel: Komponenten, die extremen Bedingungen (z. B. Schweißarbeiten, Wärmebehandlung oder bestimmten Klimabedingungen) ausgesetzt sind, sind anfälliger für Defekte. Ohne regelmäßige erweiterte ZfP-Inspektionen kann der Anlagenbesitzer den Zustand der Komponenten nicht genau beurteilen und ungeplante Stillstände folglich nicht verhindern. Eine gründliche Inspektion der kritischen Anlagen ist auch erforderlich, um eine genaue Lebensdauerbewertung (LTA) durchzuführen.
- Mechanische Vorgänge: Mechanische Vorgänge wie Schweißen und Wärmebehandlung können zusätzliche Risiken und Probleme für Behälter und Druckgeräte mit sich bringen.
- Volle Produktionskapazitäten: Kenntnis des aktuellen Zustands der Anlage ist notwendig, um zu entscheiden, inwieweit die Produktionskapazitäten voll ausgelastet werden können. Nur wenn der Anlagenbetreiber den Zustand der Anlage kennt, kann die Produktion ohne Gefährdung der Sicherheit gesteigert werden.
Wir helfen Ihnen, den Aufwand für planmäßige Turnarounds zu reduzieren und die HSE-Risiken zu minimieren, insbesondere während der Verlängerung der Lebensdauer Ihrer kritischen Anlagen. Wir bieten ein breites Portfolio an zerstörungsfreien erweiterten ZfP-Methoden an, damit Sie diese zentralen Herausforderungen meistern und Ihre spezifischen Ziele erreichen können.
Unsere erweiterten ZfP-Methoden: Erhöhung der Zuverlässigkeit Ihrer Anlagen mit unseren präzisen Inspektionen bei laufendem Betrieb
Je nach zu erwartendem Verschleiß sowie der Geometrie, der Dicke und der Materialart bieten wir erweiterte ZfP-Methoden an, die auf Ihre speziellen Bedürfnisse zugeschnitten sind. Verschaffen Sie sich einen Überblick über die verschiedenen Anwendungen und unser komplettes Angebot an zerstörungsfreien Inspektionsverfahren:
/tuv-rheinland-corrosion-mapping_core_1_x.jpg)
ZfP-Methoden zur Korrosionserkennung bei laufendem Betrieb
Korrosion kann sich in vielen verschiedenen Formen manifestieren, z. B. als generelle Wandverdünnung, als örtlich begrenzter kleiner Schaden wie Lochfraß, als spaltähnliche interkristalline Korrosion entlang der Korngrenzen oder als Korrosion unter der Isolierung (CUI). Die Kenntnis des zu erwartenden Schadensbildes ist wichtig für die Auswahl der anzuwendenden Methode. Eine generelle Materialausdünnung erfordert zum Beispiel andere Methoden als eine Korrosion von Schweißnähten.
Die nachstehenden Methoden können bei laufendem Betrieb eingesetzt werden, um Korrosion zu erkennen und ihr Ausmaß zu bestimmen.
- Korrosionskartierung mit SeeScan bis 325 °C: Die Ergebnisse der Dickenmessung werden in einer leicht verständlichen topografischen farbigen Karte dargestellt.
- Phased Array Ultraschallprüfung (PAUT) bis 425 °C: Hochauflösende Methode für eine höhere Erkennungswahrscheinlichkeit.
- Ultraschallprüfung mit Beugungslaufzeittechnik TOFD (Time of Flight Diffraction) bis 485 °C: Präzise Erkennung und Größenbestimmung von Korrosionsschäden zur genauen Überwachung.
- Ultraschallprüfung (UT) zur Stichprobenprüfung bis 425 °C: Bestimmung der Dicke von Stichproben. Wird in der Regel verwendet, wenn nur generelle Korrosion zu erwarten ist.
- Langstrecken- Ultraschallprüfung (LRUT) / Guided Wave Testing (GWT) bis 350 °C: Erkennung von Korrosion und Erosion unter der Isolierung.
- Wirbelstromprüfung (PEC) bis 300 °C: Beurteilung des Zustands von Bauteilen aus kohlenstoffarmem Stahl durch Durchdringung von Isolierungen und Beschichtungen, die nicht magnetisch sind und keinen Strom leiten (d. h. ohne Entfernung der Isolierung oder Beschichtung).
- Durchstrahlungsprüfung, Digital (RT-D): Bestimmung der Materialdicke durch Erstellung eines digitalen Profils mit Hilfe einer strahlungsempfindlichen Platte, die die Daten an ein Computersystem überträgt.
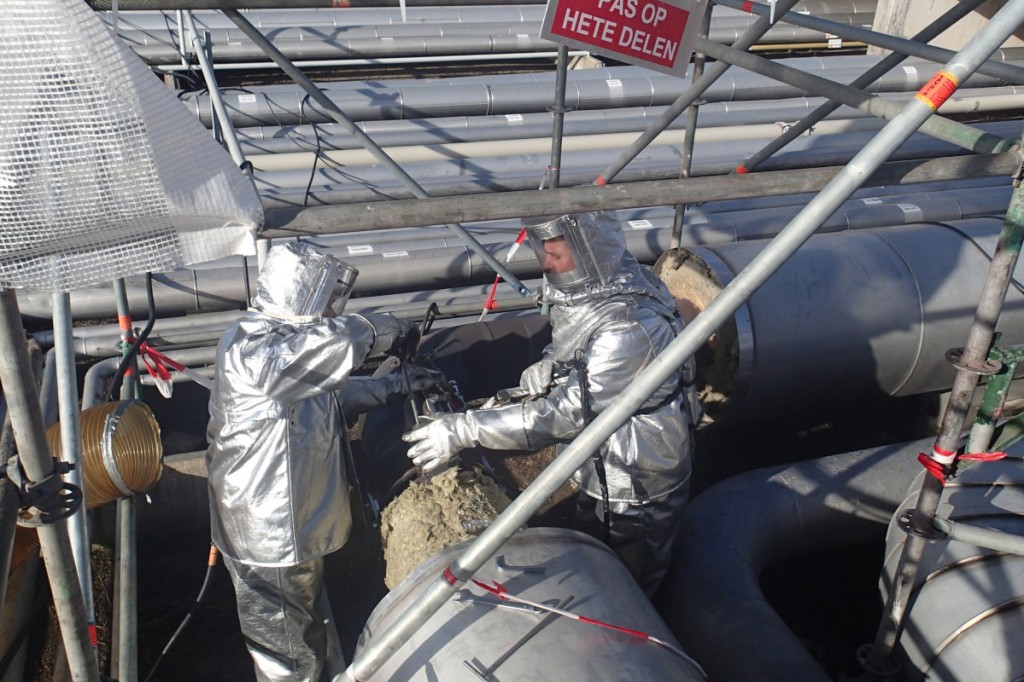
ZfP-Methoden zur Erkennung von lokalen Rissen und Leckagen bei laufendem Betrieb
Risse oder andere lokale Schäden können zu Leckagen oder sogar zum Bauteilversagen führen. Wenn rissähnliche Fehler erwartet werden, sind eine manuelle Ultraschallprüfung (UT), Time of Flight Diffraction (TOFD) oder Phased Array Prüfung (PAUT) die geeigneten Verfahren. Im Gegensatz zur routinemäßigen Ultraschallprüfung von Stumpfschweißnähten sind Mängel während des Betriebs aufgrund ihrer Kompliziertheit, ihrer schwierigen Geometrie und den Prozess der Anlage erheblich beeinflusst werden.
Schallemissionsprüfungen (AT) liefern Frühwarnungen und erkennen aktive Korrosionsrisse in einem frühen Stadium. Anzeichen für Leckagen können festgestellt werden, selbst wenn noch keine Risse aufgetreten sind. Allerdings können die Ergebnisse durch die Geometrie und den Prozess der Anlage erheblich beeinflusst werden.
Wir bieten die folgenden Methoden an, um mögliche Materialrisse bei laufendem Betrieb zu erkennen:
- Manuelle Ultraschallprüfung (UT) bis 425 °C: Die gängigste Methode für leicht erkennbare Fehler.
- Phased Array Ultraschallprüfung (PAUT) zur Prüfung von Schweißnähten bis 425 °C: Erkennung kleiner Fehler, Identifizierung und Überwachung von potenziell gefährlichem Verschleiß.
- Ultraschallprüfung mit Beugungslaufzeittechnik TOFD (Time of Flight Diffraction) zur Prüfung von Schweißnähten bis 485 °C: Präzise Erkennung und Größenbestimmung von Fehlern und Rissen zu Überwachungszwecken.
- Schallemissionsprüfung (AT) bis 400 °C: Erkennung von fortschreitenden Metallverformungen, Rissen, Fehlern und aktiver Korrosion in einem frühen Stadium.
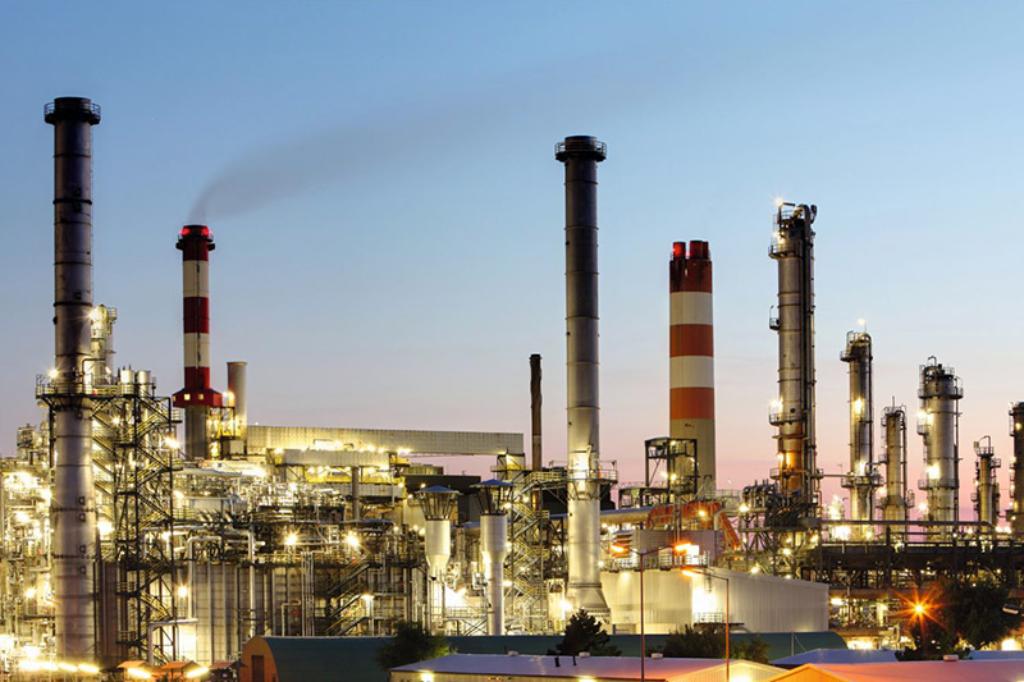
Zustandsüberwachung aus der Ferne
Durch die Erfassung und Auswertung der relevanten aktuellen Daten zur mechanischen Integrität kann der Zustand der gesamten Anlage oder einer einzelnen Komponente kontinuierlich überwacht und eine Aussage über deren Funktionsfähigkeit getroffen werden. Unsere Expertinnen und Experten setzen die neuesten Sensortechnologien ein, um eine kontinuierliche Zustandsüberwachung von Industrieanlagen aus der Ferne durchzuführen.
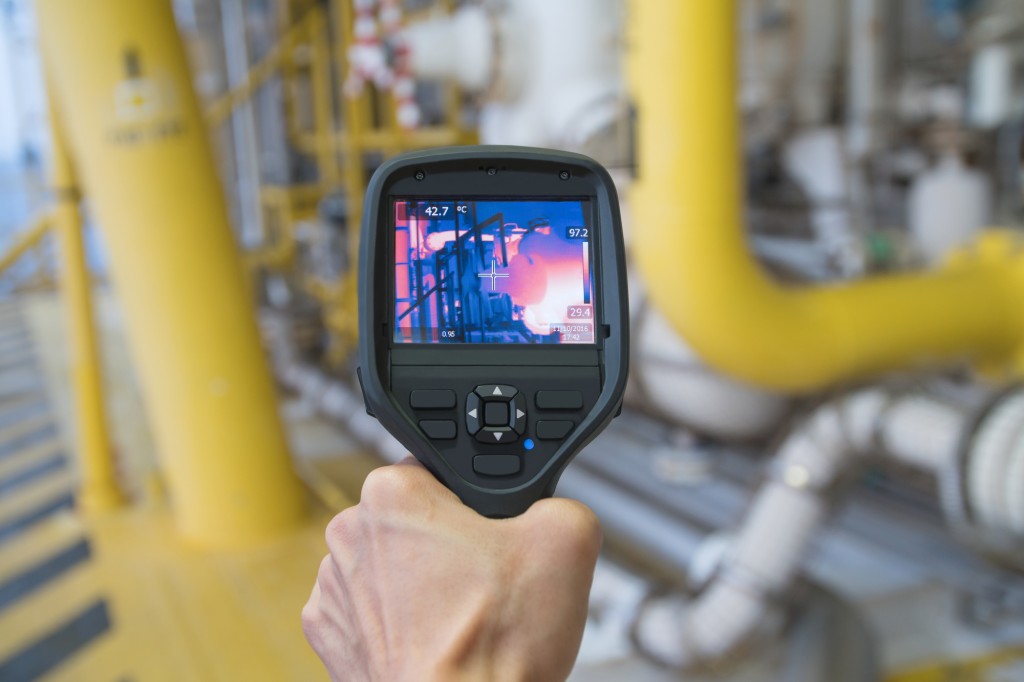
ZfP-Methoden für Wärmeverteilung
Die Wärmeverteilung auf der Oberfläche eines Bauteils kann mit einer Infrarotkamera verfolgt werden, um Auffälligkeiten zu erkennen (z. B. Hot Spots, Leckagen, Wandverdünnung, Blockierungen). Wir bieten die folgende erweiterte ZfP-Methode an:
- Thermografische Inspektion der Wärmeverteilung
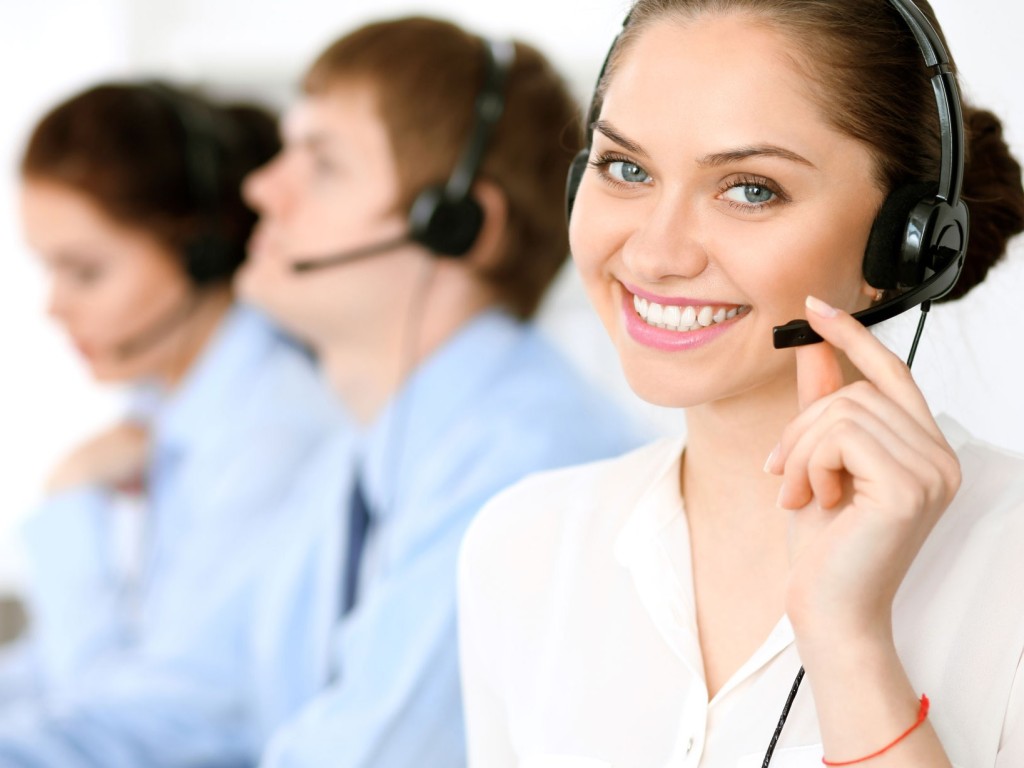