Inspection Optimization
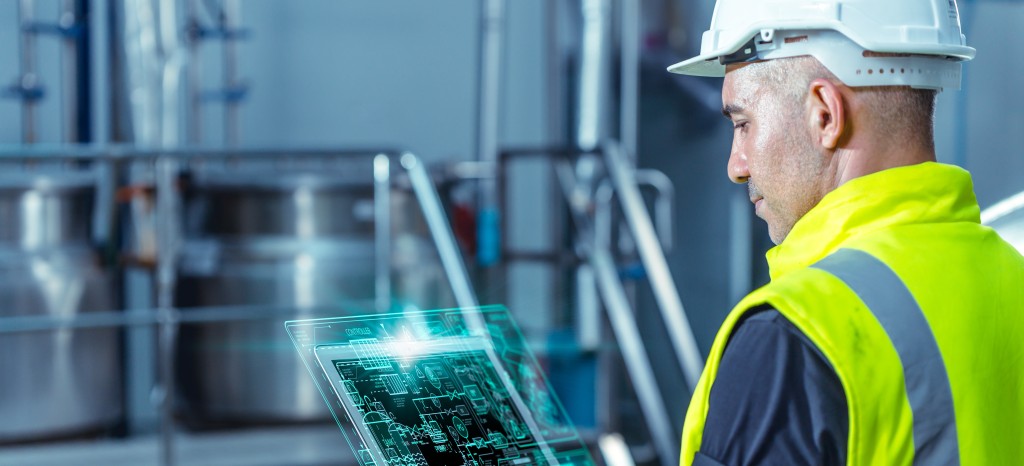
Increase your plant reliability by optimizing your inspections
Optimisation of Inspection Strategies will lead to a reduction in the turnaround scope and unplanned shutdowns, as well as effective maintenance, and increased production uptime.
It can be achieved through identification of applicable damage mechanisms specific to each individual asset, calculation of the expected degradation rate and selection of the best inspection approach(es) to detect and monitor the identified failure mechanisms.
We help you to increase your plant reliability by providing a wide range of tailor-made inspection solutions like Non-Intrusive Inspections (NII), Risk Based Inspection (RBI) support and Extended Lifetime / Fitness for Service programs.
Our NDT experts have the necessary capabilities and knowledge of both the inspection methods as well as the applicable degradation mechanisms to close the bridge between inspection preparation and the application of these inspection technologies.
Challenges: Optimization of the inspection efforts in a quick changing technical environment
The preparations and execution of the inspections are in general driven by a statutory framework. Traditionally the inspection preparation is based on general guidelines and industry practices, which could be prescriptive without taking into account the specifics of an individual asset like its actual condition and damage mechanisms.
This often leads to the use of traditional inspection methods, which do not guarantee the detection of degradation that could compromise the integrity of the assets. Degradation visible to the naked eye will be observed, but more critical changes in the material can easily being left undetected. Consequently, this ineffective inspection approach can result in extra downtime, safety risks and avoidable maintenance costs.
Here is an overview of the consequences and other relevant challenges:
- Potential health, safety and environmental (HSE) risks
- High costs due to turnaround scope and unplanned shutdowns
- Aging industrial assets
- Ineffective inspections may lead to undetected defects
- Limited in-house inspection expertise
- Increasing complexity of new NDT technologies (e.g. use of robotics, drones, AI)
Benefit from our inspection optimization services
Have a look at the benefits of using our inspection optimization services:
Our inspection optimization services: Increase reliability of your equipment with effective inspection approaches
We provide comprehensive range of services to develop the tailor-made inspection strategies specifically for your needs and assets. Our services include:
Non-Intrusive Inspections (NII)
Traditionally during the shutdown equipment is opened and cleaned in order to be inspected and then closed again. Same approach applies to those vessels that do not require cleaning, parts replacement or regeneration. As such high costs are associated with shutting down a vessel, isolating it and preparing it for an entry, followed by putting it back to service after the inspection.
Continuous uninterrupted production can be achieved by using specialist on-stream Non Intrusive Inspection (NII) solutions. This means that asset operators do not need to shut down their facilities in order to inspect the material´s properties of critical equipment.
TUV Rheinland can offer a structured procedure for an efficient implementation of Non-Intrusive Inspection in your organisation, including but not limited to:
- Definition of degradation mechanisms
- Selection of NDT techniques to detect the identified degradation
- NDT procedure preparation and/or independent review
- Result evaluation
Risk Based Inspection (RBI) support
Risk-based inspection (RBI) is an optimal maintenance business and inspection strategy used to examine equipment such as pressure vessels and piping in industrial plants.
Probability of failure is estimated on a basis of the types of degradation mechanisms and the available information of the status of the equipment. Consequence of failure can be defined for all consequences that are important, such as safety, economy and environment. Consequence of failure is evaluated as the outcome of a failure based on the assumption that such failure will occur.
TUV Rheinland can assist in the preparation of the inspection based on the output of the RBI study. This can include but not limited to:
- Inspection plan preparation
- NDT procedure preparation and/or independent review
- Result evaluation
Extended Lifetime / Fitness for Service programs
The first process step of Extended Lifetime / Fitness for Service programs is to create a model defining critical areas with possible occurring defects. Followed up by a detailed inspection report, which presents the current status of the equipment. Acceptance criteria for defects and required actions can be defined to enable keeping the equipment in service in a safe and reliable manner. Consequently, on the full assessment and possible defects found, a follow up inspection plan will be generated.
TUV Rheinland with its affiliated companies can assist in the full scope of the extended lifetime programs.
- Fatigue assessment
- Primary inspections
- Fitness for Service calculation
- Inspection follow up & Monitoring
Your experienced partner for inspection optimization
Our international network of experts develops customized inspection optimization strategies according to individual needs and environments. We work to improve the quality, safety, productivity and profitability of your assets. As a recognized, global partner, we provide you comprehensive non-destructive testing services from a single source to increase the reliability of your assets.
Contact us and put our NDT experts to work for you!
Related services
Contact
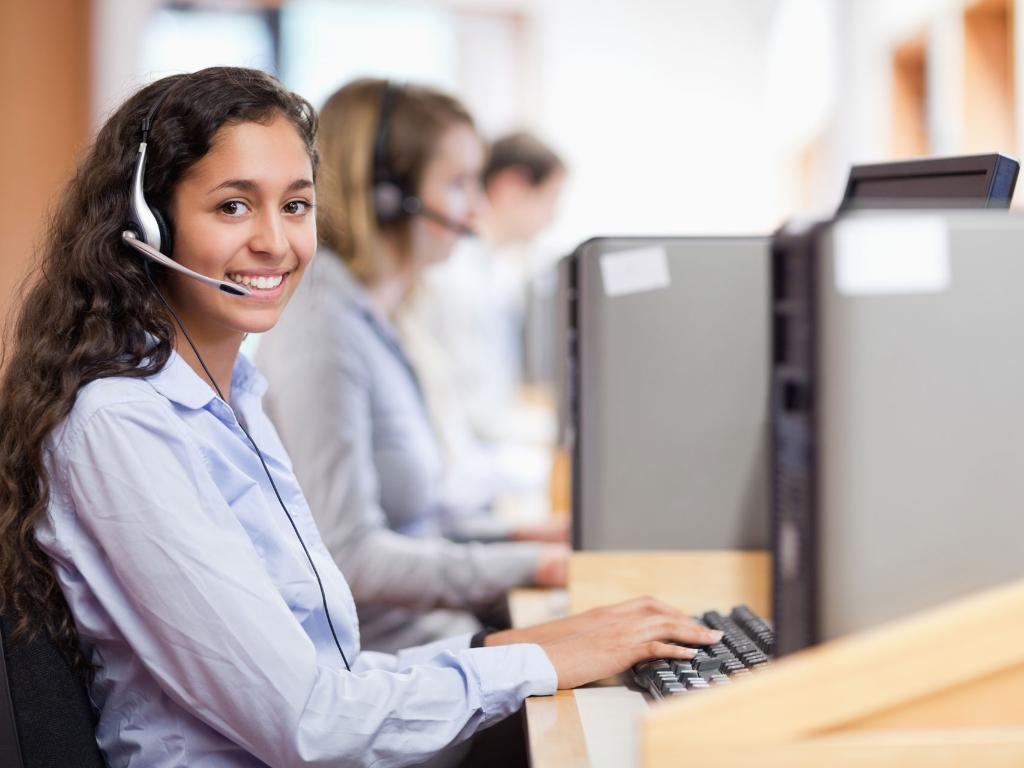